Unwinding the Mystery of Porosity in Welding: Tips for Minimizing Issues and Making Best Use Of Quality
In the detailed world of welding, porosity continues to be a persistent challenge that can dramatically affect the top quality and stability of welded joints. Comprehending the variables that add to porosity formation is critical in the quest of flawless welds. By unwinding the enigma of porosity and implementing reliable strategies for flaw reduction, welders can boost the standards of their work to accomplish premium top quality results. As we dive right into the midsts of porosity in welding, uncovering the tricks to its prevention and control will be critical for experts looking for to master the art of top quality weldments.
Comprehending Porosity in Welding
Porosity in welding, a common issue come across by welders, refers to the visibility of gas pockets or gaps in the bonded product, which can jeopardize the stability and quality of the weld. These gas pockets are generally trapped throughout the welding process due to various variables such as improper securing gas, infected base materials, or incorrect welding criteria. The formation of porosity can deteriorate the weld, making it prone to splitting and deterioration, eventually leading to architectural failures.
Comprehending the source of porosity is important for welders to properly avoid its occurrence. By acknowledging the significance of maintaining proper gas securing, ensuring the tidiness of base materials, and maximizing welding settings, welders can substantially reduce the likelihood of porosity development. Additionally, making use of techniques like preheating the base product, utilizing correct welding techniques, and carrying out comprehensive inspections post-welding can additionally aid in decreasing porosity defects. Overall, a detailed understanding of porosity in welding is important for welders to produce premium and durable welds.
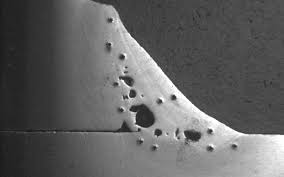
Typical Root Causes Of Porosity
When examining welding processes for potential quality issues, understanding the typical reasons of porosity is vital for preserving weld integrity and preventing structural failings. Porosity, defined by the existence of cavities or voids in the weld steel, can substantially compromise the mechanical residential or commercial properties of a welded joint.
Additionally, welding at inappropriate specifications, such as excessively high traveling speeds or currents, can create too much turbulence in the weld pool, capturing gases and triggering porosity. By resolving these typical reasons with correct gas protecting, product prep work, and adherence to ideal welding criteria, welders can reduce porosity and improve the high quality of their welds.
Strategies for Porosity Prevention
Carrying out effective safety nets is vital in minimizing the incident of porosity in welding procedures. One method for porosity avoidance is making sure proper cleaning of the base metal before welding. Contaminants such as oil, grease, corrosion, and paint can bring about porosity, so detailed cleansing making use of proper solvents or mechanical approaches is vital.

Utilizing high-quality filler products and securing gases that are appropriate for the base steel and welding procedure can substantially decrease the risk of porosity. In addition, preserving proper welding criteria, such as voltage, current, take a trip speed, and gas flow rate, is vital for porosity prevention.
Additionally, utilizing appropriate welding methods, such as preserving a constant traveling rate, electrode angle, and arc size, can assist his explanation avoid porosity (What is Porosity). Sufficient training of welders to ensure they adhere to ideal methods and high quality control procedures is also crucial in decreasing porosity issues in welding

Finest Practices for Top Quality Welds
One trick technique is preserving proper sanitation in the welding location. Completely cleaning the workpiece and surrounding location prior to welding can help minimize these problems.
Another finest method is to thoroughly pick the proper welding specifications for the details products being joined. This includes setting the right voltage, existing, take a trip speed, and shielding gas circulation price. Proper parameter option makes sure optimal weld infiltration, combination, and total high quality. Moreover, making use of premium welding consumables, such as electrodes and filler metals, can substantially impact the final weld high quality. Purchasing premium consumables can cause more powerful, a lot more durable welds with less defects. By following these best practices, welders can consistently create high-grade welds that satisfy sector standards and surpass consumer expectations.
Significance of Porosity Control
Porosity control plays an important role in ensuring the honesty and high quality of welding joints. Porosity, defined by the presence of tooth cavities or gaps within the weld steel, can significantly jeopardize the mechanical homes and structural honesty of the weld. Extreme porosity weakens the weld, making it extra prone to cracking, corrosion, and overall failure under functional tons.
Effective porosity control is important for maintaining the wanted mechanical buildings, such as toughness, find out here ductility, and durability, of the welded joint. What is Porosity. By minimizing porosity, welders can boost the overall top quality and integrity of the weld, making sure that it satisfies the performance needs of the intended application
In addition, porosity control is important for attaining the desired visual look of the weld. Too much porosity not only compromises the weld however additionally interferes with its visual appeal, which can be important in industries where looks are necessary. Proper porosity control techniques, such read here as using the right securing gas, regulating the welding parameters, and guaranteeing appropriate sanitation of the base products, are necessary for creating high-grade welds with very little issues.
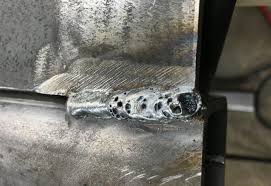
Final Thought
In final thought, porosity in welding is an usual issue that can endanger the quality of the weld. It is crucial to manage porosity in welding to make sure the honesty and toughness of the final product.